Received: August, 2010
Fluorine Notes, 2011, 75, 7-8
The Improved Preparation Method of Difluoro(fluorosulfonyl)acetyl fluoride
V.G. Barabanov, T.A. Bispen, A.N. Ilyin*, V.V. Kornilov, A.E. Krivoshein, D.D. Moldavsky, I.M. Fenichev, A.S. Vasil'ev, N.G. Zubritskaya
FSUE Russian Scientific Center "Applied Chemistry", 197198, Russia, St. Petersburg, Dobrolubov av. 14
e-mail: vbarabanov@rscac.spb.ru
*JSC "Halogen",
Russia, 614113, Perm, Lasvinskaya St., 98, E-mail: a.ilyin@halogen.ru
Abstract:Method of preparation of fluorosulfonyldifluoroacetyl fluoride involving the stages of synthesis of tetrafluoroethane-β-sultone and its subsequent isomerization was studied in details and improved.
Keywords:tetrafluoroethane-β-sultone, sulfur trioxide, fluorosulfonyldifluoroacetyl fluoride, thiethylamine
Difluoro(fluorosulfonyl)acetyl fluoride, FSO2CF2C(O)F (hereinafter isomer), due to the presence of two active functional groups, is a valuable starting material for the preparation of fluoromonomers, surfactants and other industrial products [1].
the principal method of its preparation consist in the catalytic isomerization of tetrafluoroethane-β-sultone (hereinafter sultone):
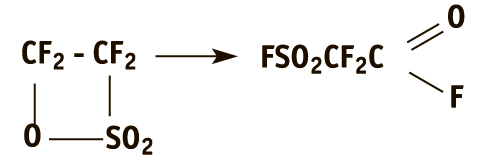
The sultone, in turn, is obtained by the reaction of tetrafluoroethylene (TFE) with sulfur trioxide:
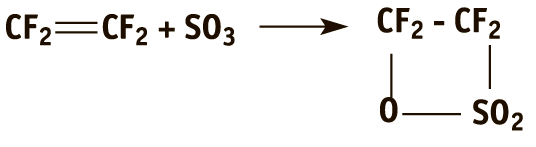
The existing methods of preparation of both sultone and isomer are hazardous and intended for purely laboratory-scale purposes [2].
The aim of the present work was to adopt the existing methods of preparation of the isomer to the commercial scales and possibilities and to make them matching the industrial scale regulations.
Preparation of the sultone
The known procedure for the preparation of the sultone consists in the reaction of a mixture of freshly distilled SO3 and TFE at 40-50 °C and pressure as high as up to 4-5 MPa. This method can not be realized in industry because at these temperatures the pressure in autoclave can rise to 4,5-6 MPa. In this case spontaneous polymerization of TFE can occur which is attended by great heat evolution and may cause the destruction of the reactor [3].
To prevent the spontaneous polymerization of TFE, stabilizers, triethylamine (TEA) being most commonly used, are added, and the monomer is kept under the pressure of not higher then 1,4 MPa.
In our first experiments on the synthesis of the sultone we used TFE purified from TEA, but after several runs with the use of purified and unpurified TFE it was found that presence of TEA did not affect the yield of the sultone, which was as high as 98,2-99,1% with 100% conversion. On the other hand, the presence of TEA made it possible to use higher pressure in the synthesis of sultone which, in turn substantially decreased the time it takes for the reaction to complete and simplified the preliminary stage of TFE treatment.
In Table 1 there are shown the results of experimental synthesis of the sultone at various pressures of TFE (180 g SO3, temperature 45 °C, stirrer rotation speed 350-400 rpm).
Table 1. Pressure dependence of the reaction time.
TFE gauge pressure, MPa |
0 |
0,1 |
0,2 |
0,3 |
0,4 |
0,5 |
0,6 |
0,8 |
1,0 |
1,2 |
Sultone synthesis bulk time, h |
10,7 |
6,7 |
5,3 |
4,7 |
3,4 |
2,4 |
1,7 |
0,8 |
0,35 |
0,25 |
As it follows from the results given in Table 1, TFE pressure of 1,2 MPa is most effective; still, pressure 0,25-0,3 was chosen from safety considerations.
The next point of the present investigation was the effect of the quality and amounts of SO3 on the reaction. Taking into account the relatively low scale of the proposed process, it was found to be not profitable to create a special unit for the production of SO3. So, the required SO3 was obtained by distilling it off from oleum. In this process, sulfuric acid is partly also distills off along with SO3, its content of the distillate may be as high as 0,2% in case of low-concentration oleum. Sulfuric acid even in trace amount may cause polymerization of sulfuric anhydride, and its content of more then 0,2% results in the increased amounts of side products, including fluorosulfonyldifluoroacetic acid FSO2CF2COOH [4].
In our experiments we used oleum with free sulfuric anhydride content of 65 and 45 % wt. On distilling off SO3 to the residual SO3 content of 18-20 wt. %, sulfuric acid content of the distillate was not higher than 0,05 wt.% [5].
With H2SO4 present in these concentrations, no formation of fluorosulfonyldifluoroacetic acid in noticeable amounts was found, and at the same time it is enough for polymerization of SO3 to proceed [6], polymerization time being highly temperature dependent. Thus, at 20°C polymerization time is 8-12 h, at 25°C it is 18-22 h, and at temperature 32°C and above polymerization time is more than 40 h.
This period of existence of SO3 in the monomeric form is quite sufficient for the formation of the sultone under normal operation conditions, but SO3 polymerizes quickly when cooled to below 25°C in an emergency. We found, however, that polymeric SO3 does react with TFE to produce the sultone, but the rate of the reaction in this case is substantially lower. The process speeds up after the consumption of about 50% of TFE amount required by stoichiometry which is probably due to better exchange and increased solubility of TFE.
Isomerization of sultone
For the isomerization of the sultone various catalysts, among them amines, metal fluorides are used, as well as heating, though TEA is the most commonly used reagent. In the initial stage of the present study we believed thermal isomerization to be the most intriguing; however, in attempting to carry out thermal isomerization we found that pre-purified (98,5 wt.%)sultone remained unchanged on heating to 100°C for several hours. Samples of lower purity decompose to form the isomer (35%), COF2, SO2 and high boiling compounds, such as tetrfluoroethane-pyrosultone
, and its isomer FSO2OSO2CFC(O)F,
along with unidentified gummy substances. Sodium fluoride showed the similar behavior: yield of the
isomer was 25 wt.%, the balance were pyrosultone and gummies.
With employing TEA as a catalyst, the sultone undergoes isomerization with yield of up to 99%. The commonly accepted procedure consist in adding TEA into the sultone at 0-30°C. The specific feature of this catalyst is that it is active only at concentrations higher than 1,5 wt.%, and at lower concentrations the reaction wouldn't go at all. The reaction proceeds with high rate (practically on the instant) and is attended with instantaneous heat evolution (estimated heat of isomerization is about 20 kJ/mol) which results in being up and, frequently, in the outburst of the reaction mixture (boiling point of the sultone is 41°C, and that of the isomer is 29°C).
The process is attended also with substantial resinification. To make the process of heat evolution more steady, we modified the regime of mixing the components, that is, the sultone was added to TEA. As a result, heat evolution in the reaction mixture was not higher than 5°C, however, this does not eliminate resinification and the necessity of washing and drying the reactor after each synthesis. Neutralization of resinous substances is a rather complicated problem which is still more objectionable in the industrial-scale production. Besides, additional equipment is needed in the industrial realization of this process.
The disadvantages of the above described catalysts led us to the necessity of a search for other compounds which could secure the highest reasonable conversion of the sultone into the isomer along with minimal formation of side products. resins in their number. With this aim, gaseous compounds as catalysts were tested to make mixing the components and isolation of the isomer from the reaction mixture more convenient and to minimize resinification.
In Table 2 there are given the results of the experiments on isomerization of the sultone (180 g) with the use of several compounds.
Table 2. Isomerization of the sultone with various catalysts.
# | Catalysts | Amount, g·mol·10-2 | Temp. °C | Time, h | Conversion, % | Isomer Yield, % | Resins,% |
1 | NF3 | 3(4,2) | 70 | 24 | 45 | 41 | - |
2 | SO2F2 | 4,5(4,4) | 75 | 24 | 23 | 19 | Traces |
3 | PF5 | 5,5(4,4) | 75 | 24 | 0 | 0 | - |
4 | NH3 | 0,25(1,4) | 40 | 4 | 100 | 63 | 27 |
5 | Trimethylamine (TMA) | 0,06(0,1) | 40 | 4 | 100 | 99,9 | Traces |
6 | Trimethylamine | 0,02(0,034) | 40 | 4 | 100 | ≥99,9 | - |
As can be seen from the results shown in Table 2, TMA is the most effective catalyst of the isomerization process.
Being on the results of the above studies, in FSUE Russian Scientific Center "Applied Chemistry" there was designed and created a pilot plant consisting of the following units: distilling off sulfuric acid anhydride, preparation of the sultone, its isomerization, and subsequent distilling to obtain the target isomer with a purity of 99,6-99,9 wt. %.
The results of these investigations are covered by the Russian Federation Patent [7].
Experimental
The reaction products were analyzed by GLC carried out with the use of a "Tsvet-800" chromatograph with FID detector, steel column 2 m, inner diameter 3 mm, liquid phase trifluoropropylmethylsilocone (SKTFT-50x) on spherochrom 0.16-0,2 mm. Carrier gas helium, flow rate 20 ml/min.
Preparation of the sultone
Into a Pyrex glass reactor flask (0,25 l) equipped with a 45 cm Vigreux column 350 g of 65% oleum was loaded, and sulfuric acid anhydride was distilled off on an air bath at 95-135°C. The anhydride was collected in reactor of synthesis of the sultone and the isomer.
The reactor with capacity of 0,8 l was made of stainless steel and equipped with a magnetic stirrer, a manometer, a reflux condenser, and a Hoffer valve for the gaseous products supply. The reactor was previously tested at excess pressure of 13 MPa. The reactor temperature in the course of the reaction was 27-32°C.
After distilling off 200 g of SO3 the reactor was closed, heated to 40-42°C and TFE was supplied from the cylinder with the pressure in the reactor maintained equal to 0,3±0,1 MPa and temperature 45-48°C. After 275 g of TFE (5% excess) was charged, the reaction mixture was stirred for more 6-8 h to achieve full consumption of SO3 (polymeric form including).
On the completion of the synthesis and blowing off the excess TFE, the reactor was cooled to 0÷+2°C, and gaseous trimethylamine (20 ml) was supplied with agitation. The mixture was heated to 40°C and kept at this temperature for 3 h, and then the isomer was distilled off to obtain the target product (456 g, 99,6 wt.% pure).
Preparation of the sultone from polymeric SO3
The distilled SO3 was kept at 13°C in the reactor for 18 h, and then TFE was supplied. It took 14 h for 140 g of TFE to be consumed, and after that the reaction mixture became liquid and capable of agitation. The remainder of TFE was supplied for 2,5 h with stirring.
The authors are sincerely grateful to N.N. Zatsepina, S.I. Ozol and V.Z. Kaufman for their assistance in this study.
Literature
- Modern Application Technology of Fluorine Compounds, Ed. by N. Ishikawa (CCMC, Tokyo, 1981; Mir, Moscow, 1984)
- Syntheses of Organofluorine Compounds (in Russian), I.L. Knunyants and G.G. Yakobson (editors). M., Khimiya, 1973, p. 77
- B.N. Maximov, V.G. Barabanov, I.L. Serushkin, at al. Industrial Organofluorine Compounds (in Russian). Leningrad, Khimiya , 1990, p. 268
- Knuniаnts I.L., Sokolski G.А. Angew. Chem. Int. Ed. 1972. V. 11. N 7. P. 583-595.
- A.G. Amelin, Production if Sulfuric Acid (in Russian), M., Khimiya, 1967, p. 437
- B.V. Nekrasov, Fundamental of General Chemistry (in Russian), M., Khimiya, 1973, p. 337
Recommended for publication by A.N. Ilyin
Fluorine Notes, 2011, 75, 7-8